News just in...
It's official, the gears are turning and the dies are cutting - production has begun! We had a soft start to production at the beginning of the week, slowly ramping up towards Friday when we gave the green light to die cut our entire pallet of recycled polypropylene. This feels like a momentous milestone we have reached, but it's not been without it's challenges! Die cutting may seem like a fairly straight forward manufacturing process, however it is somewhat of a dark art as we've learned over the last few months. Without the expert knowledge and perseverance of our manufacturing partner we may never have reached this stage.
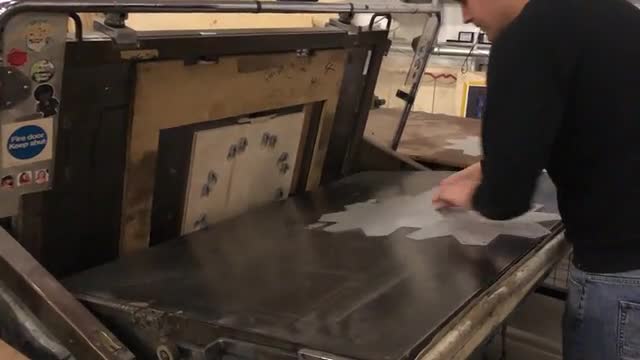
The video shows one of the last die cutting operations where holes are punched into the net shape.
Production Tooling
As promised, we want to share our final production tooling designs with you and the optimisation we have done to ensure minimal waste material. We have split production into 5 separate tools - one large tool which cuts out all the individual blanks and 4 individual tools which add the details to each POTR Pot.
Tool 1 is the largest tool in the line up - the pattern is designed to completely fill one recycled polypropylene sheet (there is only 1mm clearance to the edge of the sheet at the tightest points!). Any scrap material is recycled, feeding back into our circular manufacturing process.


Once all of the blanks are cut out using Tool 1, fold line details are added to the small and large pots using tools 2 and 3. Die cutting the blanks one at a time is slightly more time consuming but ensures accuracy between different operations.

The final two tools simply punch the holes into the net shapes and hey-presto you have yourself a POTR Pot!
The Dark (but colourful) Art of Die Cutting
One of the technical challenges we faced with such a large die cutting tool was achieving even pressure distribution across the cutting bed. Given our polypropylene sheet is only 0.75mm thick, a subtle change in pressure can mean the difference between not cutting enough or cutting all the way through the sheet! The solution? Carefully placed electrical tape!

This rather attractive multi colour pattern is no accident - each colour of tape is a different thickness resulting in different pressures being applied by each cutting blade when placed beneath our polypropylene sheet. Trial and error and a whole load of perseverance by our manufacturing partner resulted in just the right pressure distribution across each sheet!

In other news...
We've added a handy new design feature into both POTR Pot sizes - a max water level indicator! A simple embossed line has been added to one of the central triangles on each pot to achieve this.
Since our last update we have also been iterating the design of our POTR Press to make the folding process as efficient as possible. An outer structure has been designed which helps aline the net POTR to the folding mechanism underneath. This saves time on set up freeing up more time for pressing!
That's everything we have to update you on for now - next up we have some interesting updates on our eco packaging as well as samples images of our production POTRs!
Thanks once again for your ongoing support and have an ace weekend.
Andy and Martin